5 Key Differences: Lean vs Six Sigma Explained
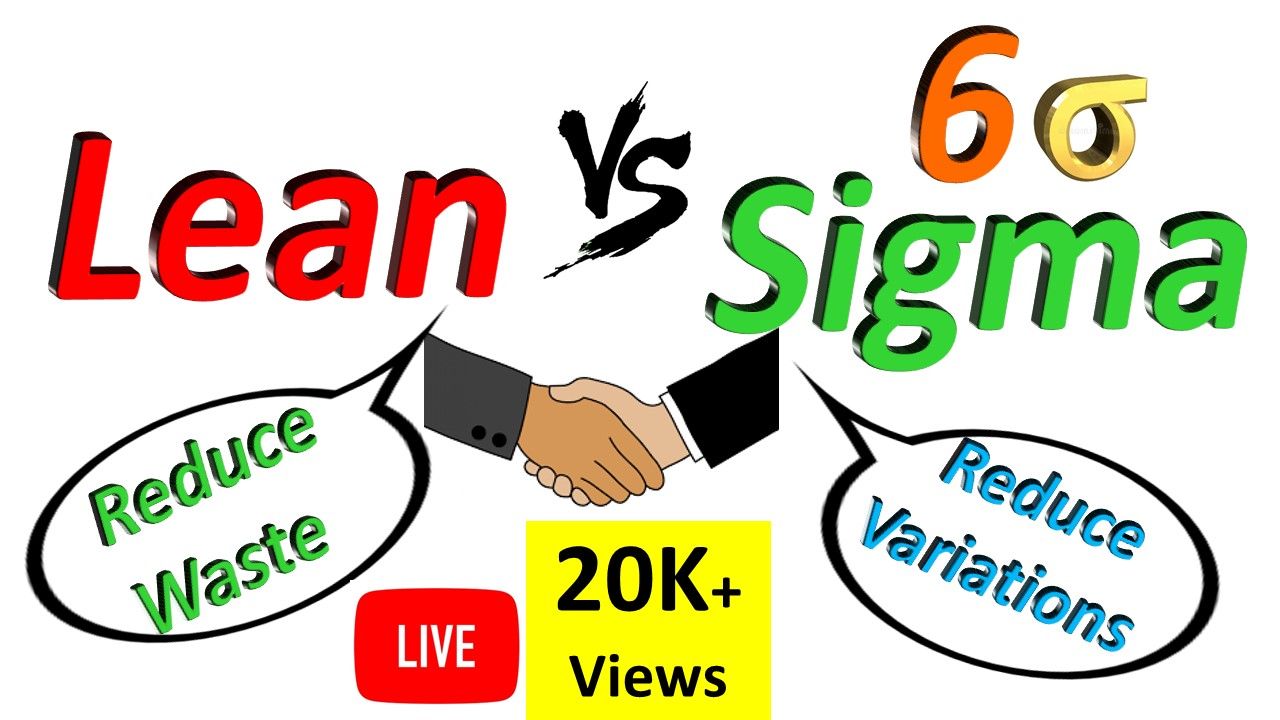
In the world of process improvement, Lean and Six Sigma are two methodologies that often dominate the conversation. While both aim to enhance efficiency, reduce waste, and improve quality, they approach these goals in distinct ways. Understanding the differences between Lean and Six Sigma is crucial for organizations looking to implement the right strategy for their specific needs. Here’s a deep dive into the 5 key differences between Lean and Six Sigma, explained with clarity and context.
1. Core Philosophy and Focus
Lean
Lean is rooted in the principles of the Toyota Production System (TPS) and focuses on eliminating waste to create value for the customer. Its core philosophy is to maximize customer value while minimizing resources. Lean identifies seven types of waste (TIMWOOD): Transport, Inventory, Motion, Waiting, Overproduction, Overprocessing, and Defects. By streamlining processes and reducing non-value-added activities, Lean aims to deliver products or services faster and more efficiently.
Six Sigma
Six Sigma, on the other hand, is a data-driven methodology that focuses on reducing variation and defects in processes. Its core philosophy is to achieve near-perfect quality by minimizing errors to a level of no more than 3.4 defects per million opportunities (DPMO). Six Sigma uses statistical tools and structured problem-solving techniques (DMAIC: Define, Measure, Analyze, Improve, Control) to identify and eliminate the root causes of defects.
Lean prioritizes waste reduction and flow, while Six Sigma focuses on defect reduction and variation.
2. Approach to Problem-Solving
Lean
Lean employs a visual and intuitive approach to problem-solving. Techniques like value stream mapping, 5S (Sort, Set in Order, Shine, Standardize, Sustain), and Kaizen (continuous improvement) are used to identify and eliminate waste. Lean emphasizes quick wins and incremental improvements, often involving frontline employees in the process.
Six Sigma
Six Sigma relies on a structured, data-driven approach. It uses statistical analysis, hypothesis testing, and tools like Pareto charts, fishbone diagrams, and control charts to identify and solve problems. Six Sigma projects are typically led by trained professionals (Green Belts, Black Belts) who follow a rigorous methodology to ensure measurable results.
Lean: Visual, intuitive, and employee-driven.
Six Sigma: Data-driven, structured, and expert-led.
3. Metrics and Measurement
Lean
Lean measures success through cycle time reduction, inventory turnover, and lead time improvements. Key performance indicators (KPIs) focus on how quickly value is delivered to the customer. For example, reducing the time it takes to produce a product from start to finish is a primary metric in Lean.
Six Sigma
Six Sigma measures success through defect rates and process capability. Metrics like DPMO, sigma levels, and process sigma are used to quantify the quality of a process. The goal is to achieve a sigma level of 6, which corresponds to 3.4 DPMO.
Lean metrics focus on speed and efficiency, while Six Sigma metrics focus on quality and consistency.
4. Implementation and Roles
Lean
Lean is often implemented as a company-wide culture rather than a project-based initiative. It encourages all employees to participate in continuous improvement activities. Roles like Lean champions, facilitators, and team leaders are common, but the emphasis is on collective effort rather than specialized roles.
Six Sigma
Six Sigma is typically implemented as project-based initiatives with defined roles and responsibilities. Trained professionals (Green Belts, Black Belts, Master Black Belts) lead projects, while executives (Champions) provide oversight. The methodology is more hierarchical and structured compared to Lean.
Aspect | Lean | Six Sigma |
---|---|---|
Implementation | Culture-driven | Project-driven |
Roles | General participation | Specialized roles |
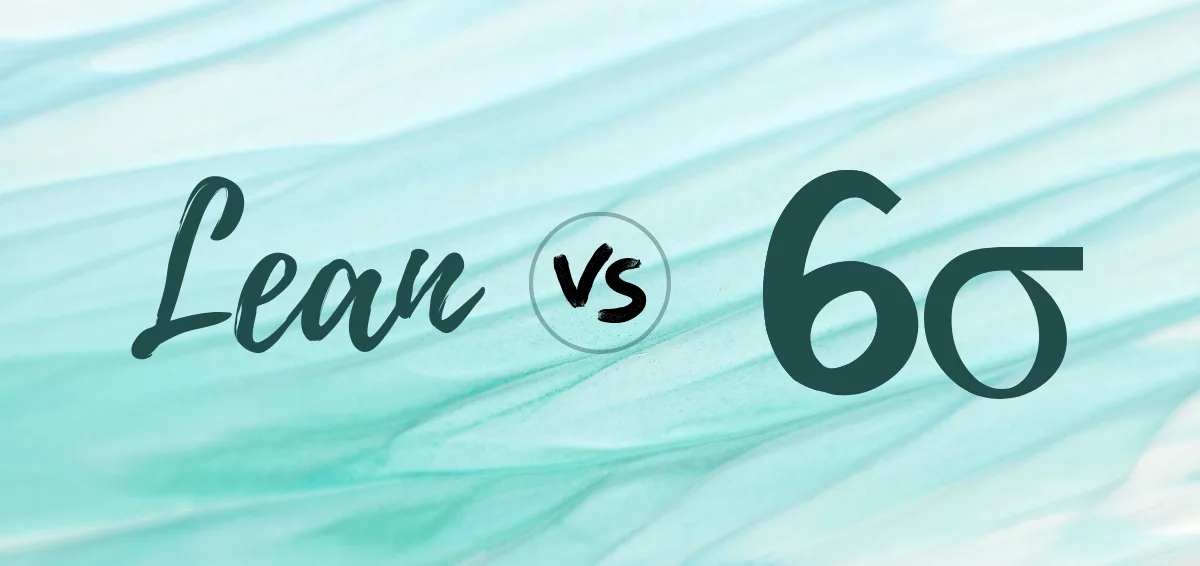
5. Scope and Application
Lean
Lean is highly effective in manufacturing and service industries where process flow and waste reduction are critical. It’s widely used in healthcare, retail, and logistics to improve efficiency and customer satisfaction. Lean’s principles are adaptable to various sectors, making it versatile.
Six Sigma
Six Sigma is particularly effective in complex, high-variation processes where defects have significant financial or safety implications. Industries like aerospace, pharmaceuticals, and finance benefit from Six Sigma’s focus on precision and quality. However, its structured approach may be less suitable for smaller organizations or processes with less variation.
Lean is versatile and broadly applicable, while Six Sigma is best suited for high-stakes, complex processes.
Lean vs Six Sigma: A Comparative Summary
Aspect | Lean | Six Sigma |
---|---|---|
Focus | Waste elimination and flow | Defect reduction and variation |
Approach | Visual and intuitive | Data-driven and structured |
Metrics | Cycle time, lead time | DPMO, sigma levels |
Implementation | Culture-driven | Project-driven |
Application | Broad (manufacturing, services) | Specific (complex, high-risk) |
FAQ Section
Can Lean and Six Sigma be used together?
+Yes, Lean and Six Sigma are often combined as Lean Six Sigma to leverage the strengths of both methodologies. Lean focuses on waste reduction and flow, while Six Sigma addresses quality and variation, creating a comprehensive approach to process improvement.
Which methodology is better for small businesses?
+Lean is generally more suitable for small businesses due to its simplicity and focus on waste reduction. Six Sigma’s structured and data-intensive approach may be too resource-intensive for smaller organizations.
How long does it take to implement Lean or Six Sigma?
+Implementation time varies. Lean can show results quickly through incremental improvements, while Six Sigma projects may take longer due to their structured and data-driven nature.
What industries benefit most from Lean?
+Lean is highly effective in manufacturing, healthcare, retail, and logistics, where process efficiency and waste reduction are critical.
What industries benefit most from Six Sigma?
+Six Sigma is particularly beneficial in industries like aerospace, pharmaceuticals, and finance, where defects have significant financial or safety implications.
Conclusion
While Lean and Six Sigma share the common goal of process improvement, their approaches, metrics, and applications differ significantly. Lean focuses on waste elimination and flow, making it versatile and broadly applicable. Six Sigma, with its data-driven focus on defect reduction, is best suited for complex, high-stakes processes. Organizations can choose one or combine both methodologies as Lean Six Sigma to achieve comprehensive and sustainable improvements. Understanding these differences is the first step toward selecting the right approach for your unique challenges.